GAS STATION WATER TREATMENT SYSTEM
Service stations, whether they are gas stations or car wash centers, have three types of water:
- The washing waters;
- Rainwater, collected on the surface of the gas station, which includes hydrocarbons;
- Wastewater, produced by the clients themselves;
- Detergents;
- Vehicle dirt (mud, sand, insects and organic matter);
- Fats.
- Decanter: Prefabricated reinforced concrete tanks that function as sand deposits, so that sand, mud, heavy particles and other pollutants with a higher density than water are concentrated at the bottom;
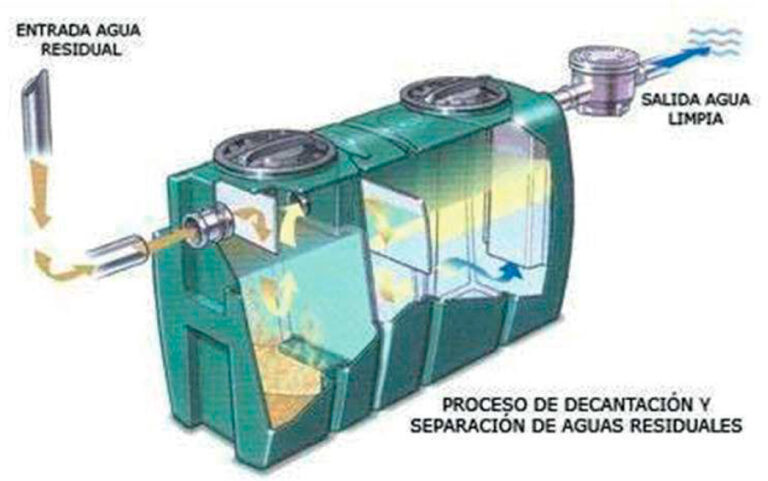
- Filtration: Process of elimination of impurities, residues and chemical substances present in the water of the washing areas. Depending on the flow to be treated, filter columns are arranged which, in their lower part, have a layer of gravel, an intermediate layer of silica sand and also an anthracite surface. Finally, the water passes through a column of activated granulated carbon to improve the quality of the treated water. Before entering the equipment, the water must go through a solids sedimentation process through a decanter, a fat separator and also a hydrocarbon separator.
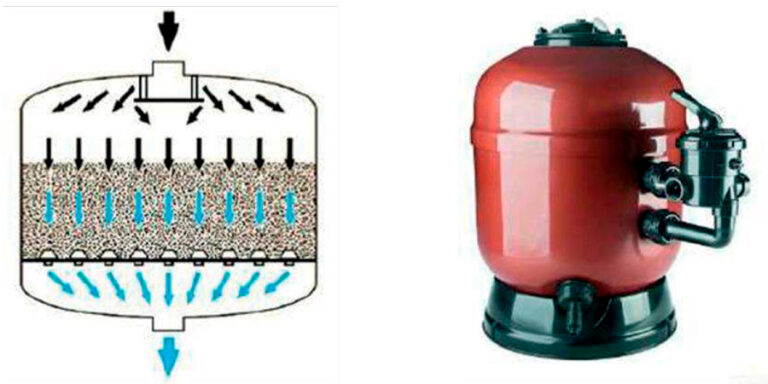
- Ultrafiltration: Ultrafiltration (UF) is a type of membrane filtration in which hydrostatic pressure forces a liquid against a semi-permeable membrane. Suspended solids and high molecular weight solutes are retained, while water and low molecular weight solutes pass through the membrane. Ultrafiltration systems dispense with the need for purifiers. This system, which uses membranes that can be submerged, reusable and air washable, offer better characteristics for the purification of drinking or waste water, promoting reuse.
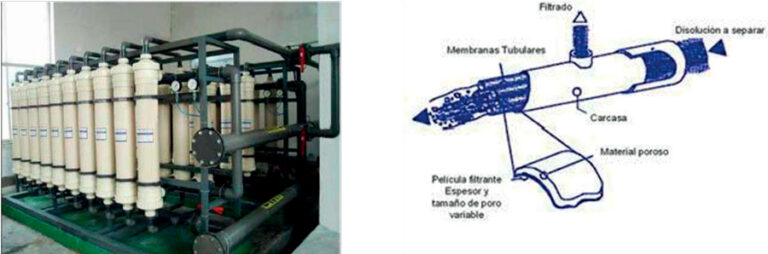
- Reverse osmosis: This equipment reduces the content of dissolved salts in the water through high pressure through a semi-permeable membrane that allows obtaining excellent quality water for washing vehicles. This process is used after ultrafiltration.
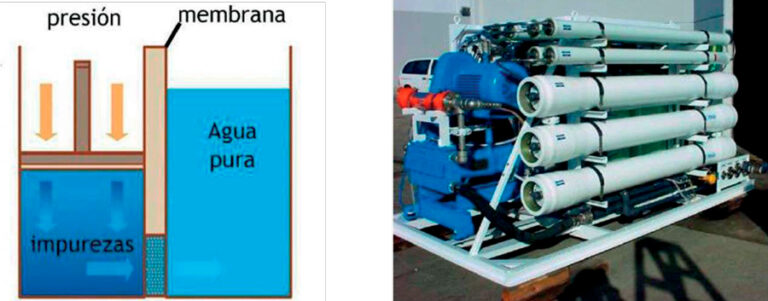
- Oil separator: For the treatment of water produced by washing the soil, or during the rainy season, the water must be treated in the same way to avoid oil spill on public roads. For this, hydrocarbon separators are used, made of reinforced concrete, reinforced with fiberglass or polyester, composed of a coalescing filter and an automatic plugging, which ensure a final discharge of the water that contains less than 5 ppm of hydrocarbons. To ensure the best performance it is necessary to complete the pre-installation with a decanter for the separation of sand and solids in the first compartment.
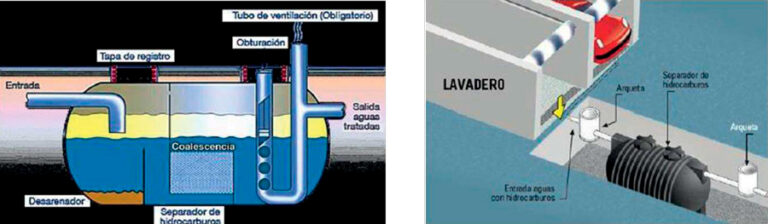
- Grease separator: If the station has a restaurant service, a grease separator must be installed, whose function is to prevent the discharge of contaminated water into the environment. The function of a grease filter is to prevent grease, oils, and other solids from ending up in sewer systems. Therefore, it separates and stores the waste and only lets clean water through. The outlet water is treated together with the wastewater from the sanitary facilities, and other cleaning services located at the station itself, in a WWTP MBR.
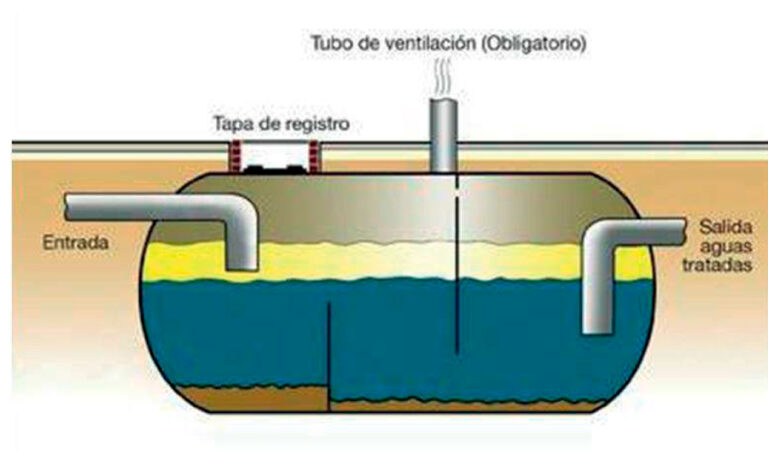
- MBR: The term membrane bio-reaction (MBR) refers to the combination of a membrane separation process. Derived from the classic activated sludge treatment system by inserting a membrane module instead of the sedimentation tank. MBRs are applicable to municipal and industrial wastewater treatment. The advantages of an MBR compared to conventional activated sludge treatment is the elimination of the need for a secondary decanter, obtaining high-quality effluents perfect for reuse, as well as the operation of a reactor with high concentrations of solids, which resulting in reduced footprint and increased treatable volumetric loads.
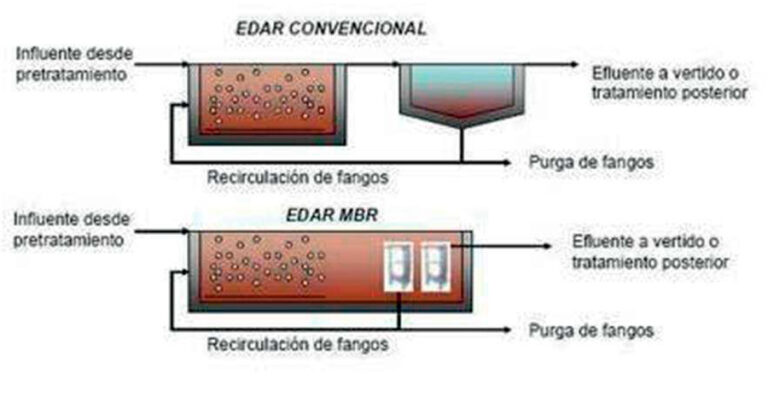
Through these systems, and due to the level of wastewater contamination, it is possible to design and build treatment plants to achieve the necessary water quality results for later use.
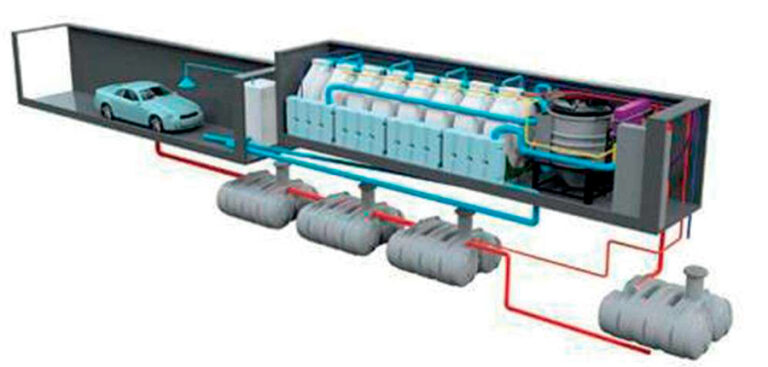